Sperrholz besteht aus drei oder mehr dünnen Holzschichten, die mit Klebstoff verbunden sind. Jede Holzschicht bzw. jedes Lagenholz ist üblicherweise so ausgerichtet, dass die Maserung im rechten Winkel zur benachbarten Schicht verläuft, um die Schrumpfung zu reduzieren und die Festigkeit des fertigen Stücks zu verbessern. Sperrholz wird meist zu großen, flachen Platten gepresst, die im Bauwesen verwendet werden. Andere Sperrholzstücke können für den Einsatz in Möbeln, Booten und Flugzeugen zu einfachen oder zusammengesetzten Kurven geformt werden.
Die Verwendung dünner Holzschichten als Baumaterial geht auf etwa 1500 v. Chr. zurück, als ägyptische Handwerker dünne Stücke dunklen Ebenholzes an der Außenseite eines Zedernholzsarges befestigten, der im Grab von König Tutanchamun gefunden wurde. Diese Technik wurde später von den Griechen und Römern zur Herstellung edler Möbel und anderer Dekorationsgegenstände verwendet. Im 17. Jahrhundert wurde die Kunst, Möbel mit dünnen Holzstücken zu verzieren, als Furnieren bekannt, und die Stücke selbst wurden als Furniere bezeichnet.
Bis ins späte 18. Jahrhundert wurden die Furnierstücke ausschließlich von Hand geschnitten. 1797 meldete der Engländer Sir Samuel Bentham Patente für mehrere Maschinen zur Furnierherstellung an. In seinen Patentanmeldungen beschrieb er das Konzept, mehrere Furnierschichten mit Leim zu einem dickeren Stück zu laminieren – die erste Beschreibung dessen, was wir heute Sperrholz nennen.
Trotz dieser Entwicklung dauerte es fast hundert Jahre, bis Schichtholz außerhalb der Möbelindustrie kommerziell genutzt wurde. Um 1890 wurde Schichtholz erstmals für den Türenbau verwendet. Mit steigender Nachfrage begannen mehrere Unternehmen mit der Produktion von mehrschichtigem Schichtholz – nicht nur für Türen, sondern auch für den Einsatz in Eisenbahnwaggons, Bussen und Flugzeugen. Trotz dieser zunehmenden Nutzung erzeugte die Verwendung von „geklebtem Holz“, wie manche Handwerker es sarkastisch nannten, ein negatives Image für das Produkt. Um diesem Image entgegenzuwirken, trafen sich die Schichtholzhersteller und einigten sich schließlich auf den Begriff „Sperrholz“ zur Beschreibung des neuen Materials.
1928 wurden in den USA die ersten Sperrholzplatten in Standardgröße (1,2 m x 2,4 m) als Baumaterial eingeführt. In den folgenden Jahrzehnten ermöglichten verbesserte Klebstoffe und neue Produktionsmethoden die Verwendung von Sperrholz für eine Vielzahl von Anwendungen. Heute ersetzt Sperrholz Schnittholz für viele Bauzwecke, und die Sperrholzherstellung hat sich zu einer milliardenschweren weltweiten Industrie entwickelt.
Die äußeren Schichten von Sperrholz werden als Vorder- und Rückseite bezeichnet. Die Vorder- und Rückseite ist die sichtbare Oberfläche, während die Rückseite ungenutzt oder verborgen bleibt. Die mittlere Schicht wird als Kern bezeichnet. Bei Sperrholz mit fünf oder mehr Lagen werden die Zwischenschichten als Querbänder bezeichnet.
Sperrholz kann aus Harthölzern, Weichhölzern oder einer Kombination aus beiden hergestellt werden. Zu den gängigen Harthölzern gehören Esche, Ahorn, Mahagoni, Eiche und Teak. Das in den USA am häufigsten zur Herstellung von Sperrholz verwendete Weichholz ist Douglasie, obwohl auch verschiedene Kiefern-, Zeder-, Fichten- und Redwood-Arten verwendet werden.
Verbundsperrholz hat einen Kern aus Spanplatten oder Massivholzstücken, die Kante an Kante verbunden sind. Die Vorder- und Rückseite sind mit Sperrholzfurnier versehen. Verbundsperrholz wird dort eingesetzt, wo sehr dicke Platten benötigt werden.
Die Art des Klebstoffs, mit dem die Holzschichten miteinander verbunden werden, hängt vom jeweiligen Verwendungszweck des fertigen Sperrholzes ab. Weichholzsperrholzplatten für den Außenbereich werden aufgrund ihrer hervorragenden Festigkeit und Feuchtigkeitsbeständigkeit üblicherweise mit Phenol-Formaldehyd-Harz als Klebstoff verwendet. Weichholzsperrholzplatten für den Innenbereich können mit Blutprotein- oder Sojaprotein-Klebstoff hergestellt werden. Die meisten Weichholzplatten für den Innenbereich werden jedoch heute mit demselben Phenol-Formaldehyd-Harz hergestellt wie die Außenplatten. Hartholzsperrholz für den Innenbereich und den Möbelbau wird üblicherweise mit Harnstoff-Formaldehyd-Harz hergestellt.
Für manche Anwendungen werden Sperrholzplatten benötigt, die mit einer dünnen Schicht aus Kunststoff, Metall oder harzgetränktem Papier oder Gewebe auf Vorder- oder Rückseite (oder beiden) verklebt sind, um die Oberfläche zusätzlich feuchtigkeits- und abriebfest zu machen oder die Farbbeständigkeit zu verbessern. Solches Sperrholz wird als Überschichtsperrholz bezeichnet und findet häufig Anwendung im Bauwesen, im Transportwesen und in der Landwirtschaft.
Andere Sperrholzplatten können mit einer flüssigen Beize beschichtet werden, um den Oberflächen ein fertiges Aussehen zu verleihen, oder sie können mit verschiedenen Chemikalien behandelt werden, um die Flammbeständigkeit oder Fäulnisbeständigkeit des Sperrholzes zu verbessern.
Es gibt zwei große Sperrholzklassen, jede mit ihrem eigenen Klassifizierungssystem.
Eine Klasse ist die der Bau- und Industriesperrhölzer. Sperrhölzer dieser Klasse werden vor allem wegen ihrer Festigkeit verwendet und nach ihrer Belastbarkeit und der Qualität des Furniers auf Vorder- und Rückseite klassifiziert. Die Belastbarkeit kann je nach Leimart innen oder außen liegen. Furnierqualitäten gibt es in den Klassen N, A, B, C und D. Klasse N weist nur wenige Oberflächenfehler auf, während Klasse D zahlreiche Äste und Risse aufweisen kann. Beispielsweise wird Sperrholz für Unterböden in Häusern der Klasse „Innen-CD“ zugeordnet. Das bedeutet, es hat eine C-Oberfläche und eine D-Rückseite, und der Leim ist für den Einsatz in geschützten Bereichen geeignet. Die inneren Lagen allen Bau- und Industriesperrholzes bestehen unabhängig von der Klassifizierung aus Furnier der Klasse C oder D.
Die andere Sperrholzklasse ist Hartholz und Dekorsperrholz. Sperrhölzer dieser Klasse werden hauptsächlich wegen ihrer Optik verwendet und nach absteigender Feuchtigkeitsbeständigkeit in Technisch (Außen), Typ I (Außen), Typ II (Innen) und Typ III (Innen) eingeteilt. Ihre Deckfurniere sind nahezu fehlerfrei.
Größen
Sperrholzplatten haben Dicken von 1,6 mm bis 76 mm. Die gängigsten Dicken liegen zwischen 6,4 mm und 19,0 mm. Obwohl Kern, Querbänder sowie Vorder- und Rückseite einer Sperrholzplatte aus unterschiedlich dicken Furnieren bestehen können, muss die Dicke der einzelnen Furniere in der Mitte ausgeglichen sein. So müssen beispielsweise Vorder- und Rückseite gleich dick sein. Ebenso müssen die oberen und unteren Querbänder gleich dick sein.
Die gängigste Größe für Sperrholzplatten im Hochbau beträgt 1,2 m Breite und 2,4 m Länge. Weitere gängige Breiten sind 0,9 m und 1,5 m. Die Längen variieren von 2,4 m bis 3,6 m in Schritten von 0,3 m. Für spezielle Anwendungen wie den Bootsbau können größere Platten erforderlich sein.
Die zur Herstellung von Sperrholz verwendeten Bäume haben in der Regel einen kleineren Durchmesser als die zur Herstellung von Schnittholz verwendeten. Meistens wurden sie auf Flächen gepflanzt und gezüchtet, die dem Sperrholzunternehmen gehören. Diese Flächen werden sorgfältig bewirtschaftet, um das Baumwachstum zu maximieren und Schäden durch Insekten oder Feuer zu minimieren.
Hier ist eine typische Abfolge von Arbeitsschritten für die Verarbeitung von Bäumen zu standardmäßigen Sperrholzplatten mit den Abmessungen 4 x 8 Fuß (1,2 x 2,4 m):
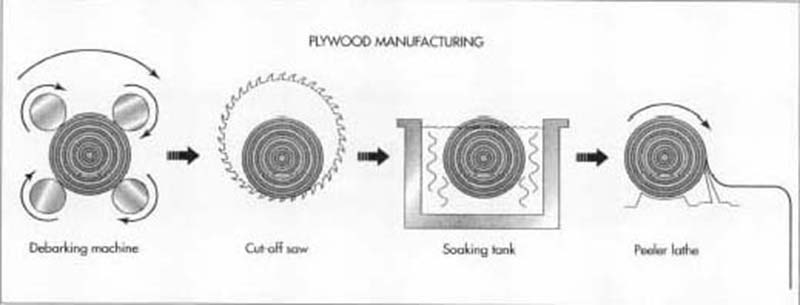
Die Stämme werden zunächst entrindet und anschließend in Schälblöcke geschnitten. Um die Blöcke in Furnierstreifen zu schneiden, werden sie zunächst gewässert und anschließend in Streifen geschält.
1 Ausgewählte Bäume in einem Gebiet werden als fällend markiert. Das Fällen kann mit benzinbetriebenen Kettensägen oder mit großen hydraulischen Scheren erfolgen, die an der Vorderseite von Radfahrzeugen, sogenannten Holzfällern, montiert sind. Die Äste werden mit Kettensägen von den umgestürzten Bäumen entfernt.
2 Die zugeschnittenen Baumstämme werden mit Schleppern (Radfahrzeugen) zu einer Ladefläche transportiert. Dort werden sie auf die richtige Länge zugeschnitten und auf Lastwagen verladen, die sie zum Sperrholzwerk transportieren. Dort werden sie zu langen Stapeln, sogenannten Holzstapeln, gestapelt.
3 Bei Bedarf werden die Stämme von gummibereiften Ladern von den Holzdecks aufgenommen und auf ein Kettenförderband gelegt, das sie zur Entrindungsmaschine transportiert. Diese Maschine entfernt die Rinde entweder mit scharfzahnigen Schleifrädern oder mit Hochdruckwasserstrahlen, während der Stamm langsam um seine Längsachse gedreht wird.
4 Die entrindeten Stämme werden auf einem Kettenförderer in das Sägewerk transportiert, wo sie von einer riesigen Kreissäge in etwa 2,5 bis 2,6 m lange Abschnitte geschnitten werden, aus denen sich Standardplatten mit einer Länge von 2,4 m herstellen lassen. Diese Stammabschnitte werden als Schälblöcke bezeichnet.
5 Bevor das Furnier geschnitten werden kann, müssen die Schälblöcke erhitzt und eingeweicht werden, um das Holz weicher zu machen. Die Blöcke können gedämpft oder in heißes Wasser getaucht werden. Dieser Vorgang dauert je nach Holzart, Blockdurchmesser und anderen Faktoren 12 bis 40 Stunden.
6 Die erhitzten Schälblöcke werden anschließend zur Schäldrehbank transportiert, wo sie automatisch ausgerichtet und einzeln in die Drehbank eingeführt werden. Während die Drehbank den Block schnell um seine Längsachse dreht, schält eine durchgehende Messerklinge mit einer Geschwindigkeit von 90–240 m/min ein durchgehendes Furnierblatt von der Oberfläche des rotierenden Blocks ab. Sobald der Durchmesser des Blocks auf etwa 230–305 mm (3–4 Zoll) reduziert ist, wird das verbleibende Holzstück, der sogenannte Schälkern, aus der Drehbank ausgeworfen und ein neuer Schälblock eingeführt.
7 Die lange Furnierplatte, die aus der Schäldrehbank kommt, kann sofort weiterverarbeitet oder in langen, mehrstöckigen Schalen gelagert oder auf Rollen gewickelt werden. Im nächsten Schritt wird das Furnier in brauchbare Breiten, üblicherweise etwa 1,4 m, geschnitten, um daraus serienmäßige Sperrholzplatten mit einer Breite von 1,2 m herzustellen. Gleichzeitig suchen optische Scanner nach Abschnitten mit unzulässigen Mängeln. Diese werden ausgeschnitten, sodass Furnierstücke mit einer Breite unter der Standardbreite übrig bleiben.
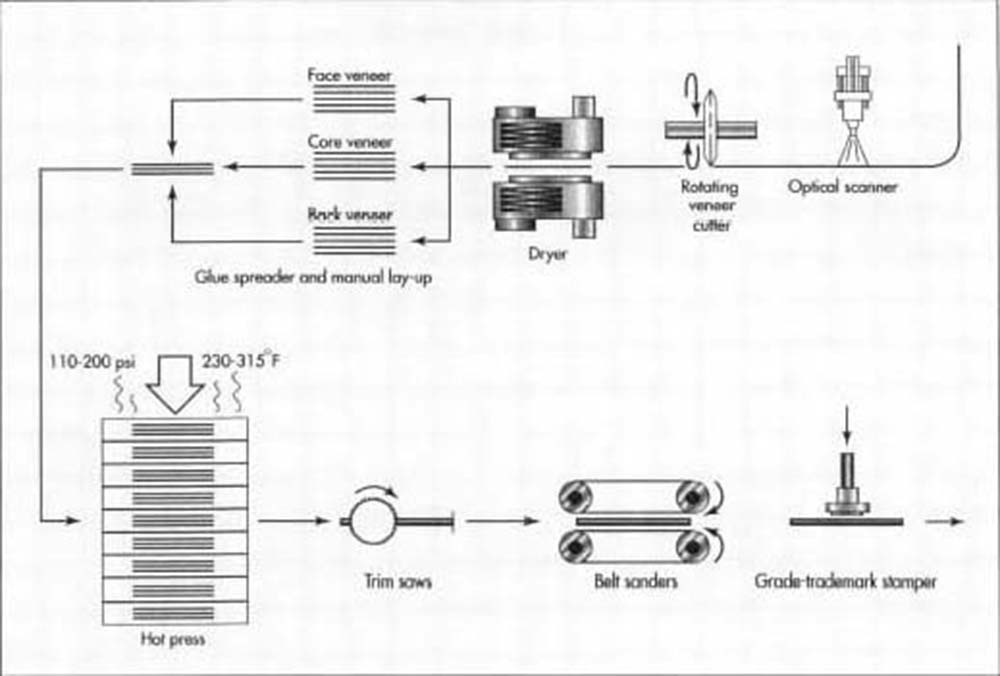
Die nassen Furnierstreifen werden zu einer Rolle gewickelt, während ein optischer Scanner alle unzulässigen Mängel im Holz erkennt. Nach dem Trocknen wird das Furnier sortiert und gestapelt. Ausgewählte Furnierabschnitte werden zusammengeklebt. Eine Heißpresse versiegelt das Furnier zu einem massiven Stück Sperrholz, das zugeschnitten und geschliffen wird, bevor es mit der entsprechenden Sortierung versehen wird.
8 Anschließend werden die Furnierabschnitte nach Güteklassen sortiert und gestapelt. Dies kann manuell oder automatisch mithilfe optischer Scanner erfolgen.
9 Die sortierten Abschnitte werden in einen Trockner gegeben, um ihren Feuchtigkeitsgehalt zu reduzieren und sie schrumpfen zu lassen, bevor sie zusammengeklebt werden. Die meisten Sperrholzwerke verwenden einen mechanischen Trockner, in dem die Stücke kontinuierlich durch eine beheizte Kammer laufen. In einigen Trocknern werden heiße Luftstrahlen mit hoher Geschwindigkeit über die Oberfläche der Stücke geblasen, um den Trocknungsprozess zu beschleunigen.
10 Die Furnierabschnitte werden nach der Qualität sortiert gestapelt. Unterbreite Abschnitte werden mit Klebeband oder Leim zusätzlich mit Furnier versehen, um sie für die Innenlagen zu verwenden, wo Aussehen und Festigkeit weniger wichtig sind.
11 Die Furnierabschnitte, die quer eingebaut werden sollen – der Kern bei dreilagigen Platten oder die Querbänder bei fünflagigen Platten – werden in Längen von etwa 1,3 m geschnitten.
12 Sobald die entsprechenden Furnierabschnitte für eine bestimmte Sperrholzreihe zusammengestellt sind, beginnt der Prozess des Auflegens und Verleimens der Teile. Dies kann manuell oder halbautomatisch mit Maschinen erfolgen. Im einfachsten Fall von dreischichtigen Platten wird das Rückseitenfurnier flach ausgelegt und durch einen Leimauftragsapparat geführt, der eine Schicht Leim auf die Oberseite aufträgt. Die kurzen Abschnitte des Kernfurniers werden dann quer auf die verleimte Rückseite gelegt, und die gesamte Platte durchläuft den Leimauftragsapparat ein zweites Mal. Schließlich wird das Deckfurnier auf den verleimten Kern gelegt, und die Platte wird mit anderen Platten gestapelt, die darauf warten, in die Presse eingelegt zu werden.
13 Die verleimten Blätter werden in eine Heißpresse mit mehreren Öffnungen geladen. Pressen können 20–40 Blätter gleichzeitig verarbeiten, wobei jedes Blatt in einen separaten Schlitz geladen wird. Sobald alle Blätter geladen sind, presst die Presse sie mit einem Druck von etwa 7,6–13,8 bar (110–200 psi) zusammen und erhitzt sie gleichzeitig auf etwa 109,9–157,2 °C (230–315 °F). Der Druck gewährleistet einen guten Kontakt zwischen den Furnierschichten, und die Hitze sorgt für die richtige Aushärtung des Leims für maximale Festigkeit. Nach 2–7 Minuten wird die Presse geöffnet und die Blätter entnommen.
14 Die Rohplatten werden anschließend durch eine Säge auf ihre endgültige Breite und Länge zugeschnitten. Hochwertigere Platten durchlaufen eine 1,2 m breite Bandschleifmaschine, die sowohl die Vorder- als auch die Rückseite schleift. Platten mittlerer Qualität werden manuell punktuell geschliffen, um raue Stellen zu beseitigen. Einige Platten werden durch eine Kreissäge geführt, die flache Rillen in die Oberfläche schneidet, um dem Sperrholz eine strukturierte Optik zu verleihen. Nach einer Endkontrolle werden alle verbleibenden Mängel behoben.
15 Die fertigen Bleche werden mit einem Gütesiegel versehen, das dem Käufer Informationen über die Bewitterungsklasse, die Güteklasse, die Fabriknummer und weitere Faktoren liefert. Bleche desselben Gütesiegels werden zu Stapeln zusammengebunden und zum Versand ins Lager gebracht.
Genau wie bei Bauholz gibt es auch bei Sperrholz kein perfektes Stück. Jedes Sperrholz weist eine gewisse Anzahl von Mängeln auf. Anzahl und Lage dieser Mängel bestimmen die Sperrholzqualität. Standards für Bau- und Industriesperrholz werden durch den Produktstandard PS1 des National Bureau of Standards und der American Plywood Association definiert. Standards für Hartholz- und Dekorationssperrholz werden durch ANSIIHPMA HP des American National Standards Institute und der Hardwood Plywood Manufacturers' Association definiert. Diese Standards legen nicht nur die Klassifizierungssysteme für Sperrholz fest, sondern spezifizieren auch Konstruktions-, Leistungs- und Anwendungskriterien.
Obwohl Sperrholz Bäume recht effizient nutzt – im Wesentlichen werden sie auseinandergenommen und zu einer stabileren, besser nutzbaren Form wieder zusammengesetzt –, entsteht im Herstellungsprozess dennoch erheblicher Abfall. Meistens werden nur etwa 50–75 % des nutzbaren Holzvolumens eines Baumes zu Sperrholz verarbeitet. Um diesen Wert zu verbessern, werden derzeit mehrere neue Produkte entwickelt.
Ein neues Produkt ist die OSB-Platte. Sie wird durch Zerkleinern des gesamten Stammes in Stränge hergestellt, anstatt ein Furnier vom Stamm abzuschälen und den Kern zu entfernen. Die Stränge werden mit Klebstoff vermischt und zu Lagen gepresst, wobei die Maserung in eine Richtung verläuft. Diese gepressten Lagen werden dann wie Sperrholz im rechten Winkel zueinander ausgerichtet und miteinander verklebt. OSB-Platten sind genauso stabil wie Sperrholz und etwas günstiger.
Veröffentlichungszeit: 10. August 2021